Two Wheeler Clutch Plate Manufacturing Plant Project Report
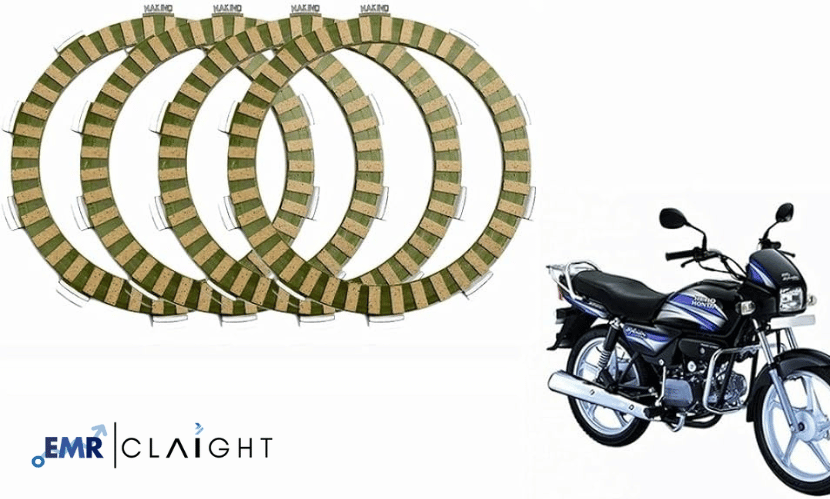
Learn about the Two Wheeler Clutch Plate Manufacturing Plant Project Report, covering the production process, raw materials, and market demand for clutch plates.
The automotive parts industry plays a pivotal role in ensuring the smooth functioning and performance of vehicles. Among the many essential components in motorcycles and scooters, the Two Wheeler Clutch Plate is one of the most important. The Two Wheeler Clutch Plate Manufacturing Plant Project Report explores the processes involved in setting up a manufacturing facility dedicated to producing clutch plates for two-wheelers, which are critical for ensuring smooth gear shifting and efficient power transmission in motorcycles.
Clutch plates, typically made of friction material, are essential for the functioning of the clutch system in two-wheelers. As the global two-wheeler market grows, the demand for high-quality, durable, and efficient clutch plates increases. This article delves into the manufacturing process, raw materials, market demand, and other critical factors to consider when setting up a two-wheeler clutch plate manufacturing plant.
Market Demand and Industry Trends
The global market for two-wheelers has seen substantial growth over the years, driven by increasing urbanization, rising disposable income, and the growing demand for fuel-efficient transportation. As the two-wheeler industry expands, so does the need for high-quality components like clutch plates that ensure the smooth operation and performance of the vehicle.
Clutch plates play a key role in the transmission system of motorcycles and scooters, helping to transmit power from the engine to the wheels while enabling smooth gear shifts. With the increasing popularity of motorcycles and scooters, particularly in emerging markets like Asia-Pacific, Latin America, and parts of Africa, the demand for clutch plates is expected to rise steadily. Additionally, the focus on producing more efficient and long-lasting components has prompted manufacturers to seek high-performance materials for clutch plates.
Another driving factor for the growth of the clutch plate market is the increasing focus on improving the performance of two-wheelers. As motorcycles become more technologically advanced, there is a greater emphasis on the quality of components such as clutch plates to ensure smooth and efficient operation. With this growing demand, setting up a manufacturing plant for two-wheeler clutch plates can be a lucrative business opportunity.
Get a Free Sample Report with Table of Contents@ https://www.expertmarketresearch.com/prefeasibility-reports/two-wheeler-clutch-plate-manufacturing-plant-project-report/requestsample
Setting Up a Two Wheeler Clutch Plate Manufacturing Plant
Setting up a Two Wheeler Clutch Plate Manufacturing Plant involves several critical steps that ensure efficient production, high-quality output, and compliance with industry standards. Below is an overview of the essential considerations when establishing such a plant.
Location Selection and Facility Design
The first step in setting up a manufacturing plant is selecting the right location. Ideally, the plant should be situated near transportation routes for easy access to raw materials and distribution of finished products. Proximity to key markets or automotive hubs is beneficial for ensuring quick delivery to customers.
The plant design must prioritize operational efficiency, safety, and flexibility. The facility should include areas for raw material storage, production lines, quality control labs, packaging, and finished goods storage. A clean and controlled environment is essential to ensure product quality, especially as clutch plates are integral to vehicle safety and performance.
Raw Materials and Sourcing
The production of high-quality two-wheeler clutch plates requires several key raw materials, each contributing to the performance and durability of the final product. These materials must be sourced from reliable suppliers to ensure consistency and quality. The main raw materials used in the manufacturing of clutch plates include:
- Friction Material: The friction material is the most important component of the clutch plate. It is typically made from a combination of organic materials, metal powders, and other friction-enhancing agents. The friction material must be durable, heat-resistant, and able to withstand the pressure and stress exerted during gear shifting.
- Steel or Cast Iron: The base of the clutch plate is usually made from steel or cast iron, which provides strength and stability. The metal must be high-quality, ensuring the clutch plate can endure the mechanical stresses and forces during operation.
- Spring Steel: Used in the production of springs for clutch systems, spring steel offers flexibility and durability.
Sourcing high-quality raw materials is critical to ensuring the longevity, safety, and performance of the clutch plates. Manufacturers must establish strong relationships with suppliers and implement quality control checks to ensure the raw materials meet the required standards.
Manufacturing Process
The production of Two Wheeler Clutch Plates involves several key stages that require precision and quality control to ensure the final product is durable, functional, and safe. The main stages of the manufacturing process include:
- Material Preparation and Cutting: The first stage involves preparing and cutting the raw materials into the desired shapes and sizes. Steel or cast iron sheets are cut into discs, which will serve as the base of the clutch plate. The friction material is also prepared by mixing it with various additives to achieve the desired performance characteristics.
- Friction Material Bonding: The next step involves bonding the friction material to the steel or cast iron base. This can be done through various methods, such as adhesive bonding, pressing, or rivet attachment. The friction material must be carefully applied to ensure uniform coverage and adhesion to the base.
- Heat Treatment: After the friction material is bonded to the base, the clutch plate undergoes a heat treatment process. This step enhances the material’s strength, wear resistance, and durability by subjecting it to high temperatures. Heat treatment also helps to reduce residual stresses in the material and improve its overall performance.
- Grinding and Shaping: After heat treatment, the clutch plates are ground and shaped to achieve the desired dimensions and smoothness. Precision grinding ensures that the clutch plates have the correct thickness, flatness, and smoothness to ensure proper functionality during operation.
- Quality Control and Testing: Quality control is a crucial aspect of the manufacturing process. Each batch of clutch plates undergoes rigorous testing to ensure that they meet safety and performance standards. The tests typically include checking for dimensional accuracy, material strength, and friction properties. Additionally, the plates are inspected for any defects, such as cracks or inconsistencies in the friction material.
- Packaging and Distribution: After the clutch plates pass quality control checks, they are packaged and prepared for distribution. The packaging must protect the plates from damage during storage and transportation. Proper labeling is also essential to provide customers with information about the product’s specifications, usage instructions, and safety guidelines.
Equipment and Technology
The production of two-wheeler clutch plates requires specialized equipment for various stages of the manufacturing process. Some of the key equipment used in clutch plate manufacturing includes:
- Cutting Machines: Used for cutting the raw material into the desired shape.
- Pressing Machines: For bonding the friction material to the steel or cast iron base.
- Heat Treatment Furnaces: For subjecting the clutch plates to high temperatures to enhance their durability.
- Grinding Machines: For shaping and finishing the clutch plates.
- Quality Control Instruments: Used to test the dimensions, material strength, and friction properties of the clutch plates.
Automation and modern technology play a critical role in ensuring efficient production and maintaining high standards of product quality. Automated systems help streamline operations, reduce manual labor, and ensure that each clutch plate is consistently produced to specification.
Quality Control and Safety Measures
Quality control is essential in the manufacturing of two-wheeler clutch plates. These components are crucial to the safety and performance of motorcycles, and any defects can result in serious issues, such as poor shifting, loss of power transmission, or even accidents. Manufacturers must implement strict quality control measures at every stage of production.
Key quality control measures include testing the friction material’s performance, ensuring the clutch plates meet dimensional specifications, and verifying that the plates can withstand the mechanical stresses during operation. Additionally, each batch must be inspected for any visual defects or inconsistencies.
Safety measures are also critical due to the heavy machinery and high temperatures involved in the manufacturing process. Proper worker training, safety protocols, and protective equipment must be in place to minimize the risk of accidents and ensure a safe working environment.
Branding and Marketing Strategies
Effective branding and marketing strategies are essential to succeed in the competitive automotive parts industry. Manufacturers of two-wheeler clutch plates must focus on key selling points, such as durability, reliability, and performance. Highlighting the safety benefits of the clutch plates and their role in ensuring smooth gear shifting and power transmission can attract customers.
Marketing efforts should target motorcycle manufacturers, retailers, and consumers. Collaborations with motorcycle manufacturers or distributors can help boost visibility, while digital marketing and social media campaigns can engage a wider audience.
Explore Trending Articles:
https://www.expertmarketresearch.com/articles/top-mayonnaise-companies
https://www.expertmarketresearch.com/articles/top-4-companies-in-the-global-industrial-hemp-market
https://www.expertmarketresearch.com/articles/top-frequency-converter-companies
Distribution Channels
Two-wheeler clutch plates can be distributed through various channels, including direct sales to motorcycle manufacturers, retail partnerships, and wholesale distributors. Additionally, online platforms offer an effective way to reach individual consumers and aftermarket suppliers.
- Arts & Entertainment
- Causes
- Crafts
- Dance
- Drinks
- Film
- Health
- Food Trends
- Gaming
- Home & Garden
- Health & Fitness
- Literature
- Music & Concerts
- Networking
- Other
- Party
- Religion
- Shopping
- Sports
- Theater
- Wellness
- Cryptocurrency
- NFT Trends
- Coin update
- Lifestyle
- Business & Finance
- Entrepreneurship
- Marketing Strategies
- Personal Finance
- Investment Tips
- Industry Trends
- Technology
- Gadgets & Reviews
- Software & Apps
- Cybersecurity
- Emerging Technologies
- How-To Guides
- Ausbildung
- Movie & TV Reviews
- Celebrity News
- Book Reviews
- Personal Development
- Motivation & Inspiration
- Life Hacks
- Community & Culture
- Local Events
- Cultural Insights
- Social Issues
- Interviews & Spotlights
- Volunteering & Activism
- Science & Nature
- Animal Behavior
- Beauty Tips
- Fashion Trends
- Product Reviews
- Food & Drink
- Cooking
- Restaurant Reviews
- Travel
- Arts & Crafts
- Photography
- Workout Routines
- Parenting Tips
- News
- Tips & Tricks
- Case Studies
- Product Reviews
- Interviews
- Opinion
- Research & Insights
- Events Coverage
- Personal Stories
- Ankündigungen
- Trends & Predictions
- Guest Posts
